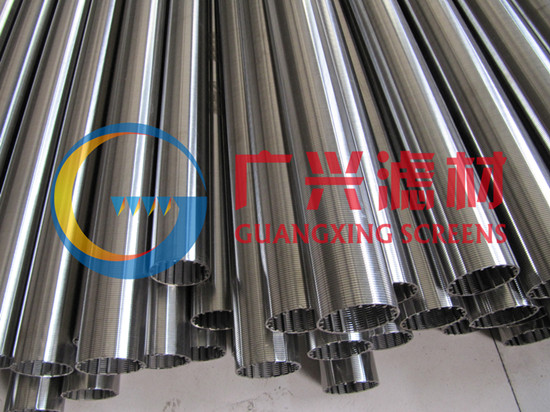
1 自动反冲洗过滤器
1.1 自动反冲洗过滤器的结构
PALL公司自动过滤系统由2个过滤罐组成,并联使用,当一个过滤罐除去液体进料中的固体悬浮颗粒时,另一个过滤罐可处于反冲洗或备用状态,准备切换使用。
自动反冲洗过滤系统每台过滤罐有247个末端为金属箍的过滤单元,每个过滤器的过滤面积为26.4 m ,滤芯是由金属丝烧结的多层滤网。该滤网采用4层结构,第1层为保护层,由较粗金属丝形成较大网孔,仅起表面保护作用;第2层为起过滤作用的精细烧结网,网孔尺寸稳定,达到拦截一定规格颗粒的目的;第3层称为排放层,使得较小颗粒能够迅速通过滤材进入下游;第4层为由很粗金属丝烧结成的具有很大网孔的支撑层,使滤材达到整体上的机械强度要求。这样的滤芯机械强度高,容污能力强[1]。
1.2 自动反冲洗过滤器的工作原理
自动反冲洗过滤系统是利用固定于其中的圆筒型过滤单元的表面收集固体颗粒的,当液体进料通过过滤器时,过滤单元表面上沉淀和富集的颗粒会形成一个颗粒层,当该颗粒层厚到一定程度时,液体流动阻力即压差变大,大到预先设定的压差时,由压差变换器检测到信号后,该颗粒层被逆向气体(反冲洗气)从过滤单元表面上除去。除下的颗粒悬浮于罐内液体中,通过过滤罐的排放管线排放掉。反冲洗时,关闭过滤罐的进出口阀,引气体到罐子顶部加压,迅速打开过滤罐的排放阀,使罐子压力降到大气压力。
1.3 自动反冲洗过滤器的优点
当自动反冲洗过滤器进出口压差超过程序设定值时,反冲洗程序自动启动。由于反冲洗排放管较粗,与进口原料管一样都为25.4 cm(10英寸),每根滤芯的目数从外至里逐渐增大,网孔逐渐变小,反冲洗时利用气体膨胀和排放阀门瞬时开启的联合效果,产生的冲击能量将滤饼完全卸除并排出滤壳外。反冲洗过程1 min可完成,从而达到较好的反冲洗效果。反冲洗采用氮气,因催化裂化装置用的原料油允许含有杂质,故吹出的废油送至催化裂化装置加以利用,且由于该系统是密闭排放,使得装置现场环境大为改善,环保合格率提高到95%以上。与原来手动切换的过滤器相比,过滤精度大大提高,使得精制反应器催化剂床层压差上升趋势得以延缓[1]。
2 存在的主要问题及原因分析
2.1 存在的主要问题
a) 随着芳烃厂加氢裂化装置运行时间的延长,自动反冲洗过滤系统出现进出口压差上升较快,运行周期缩短,严重时2 min过滤器就要切换1次,并随着工艺条件的变化而变化,不能满足装置的进料负荷。
b) 自动反冲洗过滤系统切换频繁,使得过滤器产生大量污油,增加了芳烃厂加氢裂化装置的加工损失率,影响了装置的经济性。另外,产生的污油量超出了污油罐设计的排污能力,导致过滤罐中大量的污油无法带走,影响了反冲洗效果,造成恶性循环,导致过滤周期越来越短,并对污油系统造成冲击,现场环境差且环保合格率降低,不能满足环保达标要求。再者,自动反冲洗过滤系统的频繁切换,使得滤芯需经常抽出进行煤油清洗,大大增加了保运人员的劳动强度。
2.2 原因分析
自动反冲洗过滤系统过滤周期缩短后,在送往PALL公司原料样品中发现有胶状物质,由于胶状物质是由各种不同结构的非烃化合物所构成的多分散复杂混合物体系,流动和扩散性能差。为了确定是否由于胶状物质包裹原料中的机械杂质形成滤饼,从而堵塞滤芯孔隙结构造成的,技术人员多次使用航空煤油清洗过滤器,但过滤周期并未延长,这说明胶状物质的存在并不是造成FD一101A/B过滤周期缩短的主要原因。分析自动反冲洗过滤系统滤芯的结构,知道每根滤芯是由金属丝烧结的4层结构滤网紧密结合在一起而构成的,且每层滤网之间错开一定的位置,以达到一定的过滤精度。随着自动反冲洗过滤系统使用周期的延长,滤芯在不断变化的压力作用下,各滤网层之间产生细微的变形,部分固体颗粒被嵌在滤网层间,无法随着反冲洗液排出过滤罐,进而堵塞滤芯孔隙结构,导致单台过滤器过滤面积减小,从而缩短过滤器运行周期。进一步分析原料品质,发现芳烃厂加氢裂化装置原设计加工胜利油田的轻质油品,但在实际生产中还使用了大量的来自沙特、伊朗等中东地区进口油,此进口油大都为含硫或高硫原油,且残炭、重金属含量等比较高,使芳烃厂加氢裂化装置加工的油品呈现劣质化趋势,原料粘度越来越高,*高时是设计值的5.4倍,而过滤周期与原料粘度成反比。
3 滤芯清洗
基于以上分析,2004年芳烃联合装置停车检修期间,将FD一101A/B滤芯进行器外清洗及检测。2004年6月30日,2台FD一101A/B共494根滤芯拆出、封箱,送往清洗。
3.1 预处理
为了防止待处理滤芯含有的垢油在焙烧程序中燃烧,使焙烧炉飞温,损伤滤芯的力学性能或引起晶间腐蚀,在清洗前先采用热的轻质油(柴油或煤油)浸泡滤芯,并用蒸汽吹扫,以减少滤芯附着的垢油。
3.2 清洗程序
3.2.1 焙烧
将经过预处理的滤芯放入焙烧炉内,按照图1曲线升温。为防止出现飞温,每15 min记录1次焙烧炉设定温度和实际温度。
3.2.2 水洗
待滤芯冷却到常温后,用10~15 MPa高压水枪先从滤芯外表面冲洗,接着从管内反向冲洗。
3.2.3 碱洗
在容槽中用去离子水配制15 ~20 的纯碱溶液,接着将滤芯放入溶液中加热到接近沸腾,保持1.0~1.5 h,根据需要补加水。
3.2.4 水洗
从容槽中取出滤芯,用10~15 MPa高压水枪先从滤芯外表面冲洗,接着从管内反向冲洗。
3.2.5 酸洗
将滤芯放人15 ~ 20 的硝酸溶液容槽中,加热至60~70℃ ,保持1.0~1.5 h。
3.2.6 水洗
从容槽中取出滤芯,用去离子水清洗滤芯,然后用10~15 MPa的高压水枪先从滤芯外表面冲洗,接着从管内反向冲洗。然后让滤芯在空气中晾干。
3.2.7 检测
按照图2流程进行滤芯空气通透性测定。将B阀关闭,由A 阀控制通人一定流量的仪表风,使滤芯的空气由内向外流动,测定滤芯压差。先检测1根新的同标准型号滤芯压差,记下压差。然后测定处理后的滤芯压差,并作记录。每测1根前都要观察转子流量计流量,调节流量并始终维持同一流量大小通过滤芯,使用40倍的放大镜观察滤芯样品外表面的污染物。如果被测的滤芯压差与标准滤芯的压差相差过大或没有洗干净,可重复清洗步骤。
4 滤芯清洗前后效果对比
4.1 延长了过滤周期
表1显示了滤芯清洗前后,在流通量基本相同的情况下,FD-101A/B过滤周期大幅提高,平均运行时间是原来的6倍,且压降升高较慢,保证了连续4 h的过滤周期,达到了清洗目的。
4.2 恢复了过滤质量
表2列出了新的Rigimesh型R级滤芯以及清洗后的滤芯出口固体颗粒度分布。从表2可以看出,过滤器出口颗粒总数相当,这说明与新滤芯相比,滤芯清洗后起过滤作用的精细烧结网的网孔尺寸得到了有效的恢复。
4.3 提高了环保合格率
清洗后未发生FD一101A/B切换过频的现象,减少了对污油系统造成的冲击,重污油管线很少出现正压的情况,环保合格率由原来的84.6 提高到97.4 。
4.4 提高了装置经济性
由于清洗前FD一101A/B切换过频,排放污油多达60 t/d,不仅浪费了大量的氮气,而且频频造成过滤器切换故障,装置进料中断,严重影响了装置的加工能力及安全运行,而清洗后排放的污油仅8 t/d,装置的加工损失率大大下降,提高了装置的经济性。同时,由于不再需要经常抽出滤芯进行清洗,减轻了保运人员的劳动强度。
5 结语
通过对自动反冲洗系统滤芯清洗前后的对比分析可以看出,清洗后FD一101A/B过滤质量及效率得以恢复,延长了过滤周期,达到了每4 h切换1次的目标;由于滤芯清洗后未发生过滤器切换过频的现象,减少了对污油系统造成的冲击,装置环保合格率大大提高;滤芯清洗投用后,操作人员与检修人员劳动强度大为减轻,提高了装置的经济性,保证了装置的达标及高负荷运转。